APQP (Gelişmiş Ürün Kalite Planlama) aşamaları, örnek
APQP (Gelişmiş Ürün Kalite Planlaması), İspanyolca "Gelişmiş Ürün Kalite Planlaması" olarak, endüstride, özellikle otomotivde ürün geliştirmek için kullanılan prosedür ve tekniklerin bir çerçevesidir..
Karmaşık ürünler ve tedarik zincirleri, özellikle yeni ürünler piyasaya sürüldüğünde birçok başarısızlık olasılığı sunmaktadır. APQP, yeni ürün veya süreçlerde müşteri memnuniyetini sağlamayı amaçlayan ürün ve süreçlerin tasarımı için yapılandırılmış bir süreçtir..
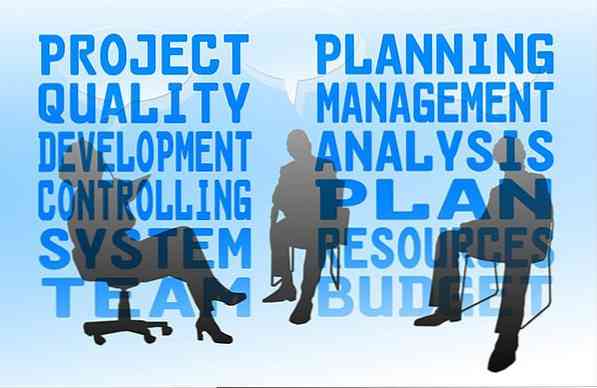
Bu yaklaşım, yeni bir ürün veya süreçteki değişikliklerle ilişkili riskleri azaltmak için araçlar ve yöntemler kullanır..
Amacı, tedarikçilerin müşteriyi tatmin edecek bir ürün veya hizmeti tasarlamalarını, farklı etkinlikler arasında iletişimi ve işbirliğini kolaylaştırmasını sağlayan standart bir ürün kalitesi gereksinimleri planı oluşturmaktır..
APQP sürecinde, pazarlama, ürün tasarımı, satın alma, üretim ve dağıtımı içeren çok işlevli bir ekip kullanılır. Bu işlem General Motors, Ford, Chrysler ve tedarikçileri tarafından ürün geliştirme sistemi için kullanılmaktadır..
indeks
- 1 Aşama
- 1.1 Aşama 1: Programın planlanması ve tanımı
- 1.2 2. Aşama: Ürünün tasarımı ve geliştirilmesi
- 1.3 Faz 3: Ürün imalat sürecinin tasarımı ve geliştirilmesi
- 1.4 Aşama 4: Proses ve ürün doğrulama
- 1.5 Aşama 5: Başlatma, Değerlendirmeler ve Sürekli İyileştirme
- 2 Örnek
- 2.1 APQP'nin nereye dahil edileceği
- 2.2 Onu kullanan endüstriler
- 3 Kaynakça
fazlar
APQP, geliştirme sürecinde bir rehber olarak ve aynı zamanda tedarikçiler ile otomotiv şirketleri arasında sonuçları paylaşmanın standart bir yolu olarak hizmet vermektedir. Beş aşamadan oluşur:
1. Aşama: Programın planlanması ve tanımı
Müşterilerin talebi, yeni bir ürünün tanıtımını veya mevcut bir ürünün revizyonunu gerektirdiğinde, ürünün tasarımı veya yeniden tasarımı hakkında tartışmalardan önce bile, planlama merkezi bir tema haline gelir..
Bu aşamada, planlama müşterinin ihtiyaçlarını ve ayrıca ürünün beklentilerini anlamaya çalışır..
Planlama faaliyetleri, müşterinin ne istediğini tanımlamak için gerekli verilerin toplanmasını ve daha sonra bu bilgilerin ürünün özelliklerini tartışmak için kullanılmasını içerir..
Ardından ürünü belirtilen şekilde oluşturmak için gereken kalite programını tanımlayabilirsiniz..
Bu çalışmanın sonucu ürün tasarımı, güvenilirlik ve kalite hedeflerini içerir.
2. Aşama: Ürün tasarımı ve geliştirme
Bu aşamanın amacı ürün tasarımını tamamlamaktır. Bu aynı zamanda ürünün uygulanabilirliğinin bir değerlendirmesinin devreye girdiği yerdir. Bu aşamadaki çalışmalardan elde edilen sonuçlar:
- Tamamlanan tasarımın gözden geçirilmesi ve doğrulanması.
- Malzeme ve ekipman gereksinimlerinin tanımlanmış özellikleri.
- Arıza ihtimalini değerlendirmek için tamamlanan tasarımın etki ve başarısızlık modunun analizi.
- Ürün prototipinin oluşturulması için oluşturulan kontrol planları.
Faz 3: Ürün imalat sürecinin tasarımı ve geliştirilmesi
Bu aşama, yeni veya geliştirilmiş ürünü üretecek üretim sürecinin planlanmasına odaklanır.
Amaç, ürünün özelliklerini ve kalitesini ve üretim maliyetlerini göz önünde bulundurarak üretim sürecini tasarlamak ve geliştirmek..
İşlem, verimliliği korurken, tüketicilerin beklenen talebini karşılamak için gerekli miktarları üretebilmelidir. Bu aşamadaki sonuçlar şunları içerir:
- İşlem akışının eksiksiz bir konfigürasyonu.
- Risklerin tanımlanması ve yönetilmesi için tüm sürecin etki ve başarısızlık modunun analizi.
- İşletme sürecinin kalite özellikleri.
- Ürünün ambalajlama ve bitirme gereksinimleri.
Aşama 4: Proses ve ürün doğrulama
Bu, üretim sürecini ve son ürünü onaylayan test aşamasıdır. Bu aşamadaki adımlar şunları içerir:
- Üretim sürecinin kapasitesinin ve güvenilirliğinin doğrulanması. Aynı şekilde, ürün kalitesinin kabul kriterleri.
- Test üretim çalışmalarının gerçekleştirilmesi.
- Uygulanan üretim yaklaşımının etkinliğini doğrulamak için ürün testi.
- Bir sonraki aşamaya geçmeden önce gerekli ayarlamaları yapın..
Aşama 5: Başlatma, Değerlendirmeler ve Sürekli İyileştirme
Bu aşamada, büyük ölçekli üretimin başlatılması, süreçlerin değerlendirilmesi ve iyileştirilmesine vurgu yaparak gerçekleşir..
Bu aşamadaki sütunlar arasında süreç değişikliklerinin azaltılması, sorunların belirlenmesi ve sürekli iyileştirmeyi desteklemek için düzeltici faaliyetlerin başlatılması vardır..
Süreç verimliliği ve kalite planlaması ile ilgili müşteri geri bildirimlerinin ve verilerin toplanması ve değerlendirilmesi de bulunmaktadır. Sonuçlar şunları içerir:
- Proses değişikliklerini azaltarak daha iyi bir üretim süreci.
- Ürün ve hizmetin müşteriye tesliminde kalitenin iyileştirilmesi.
- Müşteri memnuniyetinde iyileşme.
örnek
APQP'yi nereye dahil edersiniz?
- Kalite fonksiyonunun uygulanmasını kullanarak müşterinin sesinden gereksinimlerin geliştirilmesi.
- Proje programına entegre bir ürün kalite planının geliştirilmesi.
- Tasarımı bırakmadan önce, özel özellikleri veya anahtarları işlem tasarım faaliyetine aktaran ürün tasarım faaliyetleri. Bu yeni şekiller ve parçalar, daha sıkı toleranslar ve yeni malzemeler içerir.
- Test planlarının geliştirilmesi.
- İlerlemeyi izlemek için resmi tasarım incelemesinin kullanılması.
- Ürün tasarımı kaynağı tarafından verilen tasarım toleranslarına göre, sürecin uygun ekipman ve araçlarının planlanması, satın alınması ve montajı.
- Bir ürünün daha iyi montajı için montaj ve imalat personeli tarafından önerilerin iletilmesi.
- Potansiyel arıza riskini yöneten, bir ürünün özel özellikleri veya anahtarları veya bir prosesin parametreleri için yeterli kalite kontrollerinin oluşturulması.
- Mevcut varyasyonu anlamak ve böylece proseslerin istatistiksel kontrolü ve prosesin kapasitesi ile gelecekteki performansı tahmin etmek için stabilite ve özel özelliklerin kapasite çalışmalarının gerçekleştirilmesi..
Onu kullanan endüstriler
Ford Motor Company, 1980'lerin başında tedarikçileri için ilk gelişmiş kalite planlama kılavuzunu yayımladı ve bu, Ford tedarikçilerinin yeni ürünler için uygun önleme ve tespit kontrolleri geliştirmelerine yardımcı oldu ve böylece kurumsal kalite çalışmasını destekledi..
80'lerin sonunda, otomotiv endüstrisinin ana üreticileri APQP programlarını kullandı. General Motors, Ford ve Chrysler uyguladı ve tedarikçilerine ürün kalitesi planlama ilkelerinin ortak bir çekirdeğini oluşturmak için birleştirme gereği duydu..
APQP protokollerinin standart bir biçimde takip edilmesini sağlamak için 1990'ların başında kılavuzlar oluşturulmuştur..
Üç otomotiv üreticisinin temsilcileri ve Amerikan Kalite Kontrol Derneği, otomotiv endüstrisinde karşılıklı ilgi duyulan konular hakkında ortak bir anlayışa sahip olmak için bir grup kalite gereksinimi yarattı..
Bu metodoloji şu anda ilerici şirketler tarafından da planlama yoluyla kaliteyi ve performansı garanti etmek için kullanılmaktadır..
referanslar
- Vikipedi, özgür ansiklopedi (2018). Gelişmiş ürün kalite planlaması. Alındığı kaynak: en.wikipedia.org.
- NPD Çözümleri (2018). İleri Ürün Kalite Planlaması. Alındığı kaynak: npd-solutions.com.
- Birinci Kalite (2018). Gelişmiş Ürün Kalite Planlaması (APQP). Alınan: quality-one.com.
- Yemler (2018). APQP'nin 5 Aşaması: Temel Gereksinimlere Genel Bir Bakış. Alındığı kaynak: cebos.com.
- David Ingram (2018). İleri Ürün Kalite Planlaması. Küçük İşletmeler - Chron.com. Alındığı kaynak: smallbusiness.chron.com.